Machine Vision Systems: Connectivity's Hidden Role in Automation
From 2D to 3D: A Closer Look at Machine Vision Camera Formats and Applications
Machine vision cameras come in various formats, each designed for specific scenarios with distinct advantages. Below are some of the most common camera formats and their application scenarios.
2D cameras capture two-dimensional images, converting scenes into planar images. They are widely used in object detection, pattern recognition, measurement, and optical character recognition (OCR). Utilizing CCD or CMOS sensors to convert light into electrical signals, they are applied in automation processes across manufacturing, logistics, healthcare, robotics, and other industries.
- Area Scan Cameras
Area scan cameras, a type of 2D camera, are specifically designed to capture static images. They use an array of photosensitive elements to record light intensity, producing complete two-dimensional images. These cameras are suitable for industrial inspection and quality control, such as product appearance inspection and robotic vision systems.
- Line Scan Cameras
Line scan cameras are specifically designed to capture images of continuously moving objects line by line. They are perfect for high-resolution inspection of long, continuous materials such as fabrics and paper, as they effectively prevent motion blur. These cameras are commonly used for product inspection and defect detection on high-speed production lines.
3D cameras capture three-dimensional information about objects, measuring depth (Z-axis) in addition to length and width. They are crucial in applications requiring precise object positioning, dimensional measurement, and surface inspection. Widely used in industrial automation, robot navigation, and bin-picking scenarios, they enhance accuracy and efficiency.
- Time-of-Flight (ToF) Cameras
Time-of-flight cameras calculate object distance based on the time it takes for light to be emitted and reflected. Suitable for rapidly capturing depth images, they are applied in packaging inspection, robot guidance, and automated assembly.
- Laser Triangulation Cameras
Using lasers to measure the height and shape of object surfaces, these cameras are ideal for high-precision 3D modeling, such as precise inspection of automotive parts and industrial machinery.
- Stereo Vision Cameras
Stereo-vision cameras infer depth using images from two or more viewpoints. They are suitable for scenarios requiring precise positioning, like electronic component inspection and robot guidance.
Smart cameras integrate image capture, processing, and analysis functions into a single device, capable of real-time image processing without relying on external computers. Particularly suitable for real-time detection, classification, and quality control on production lines, they find applications in manufacturing, robotic vision, and automated inspection systems.
Thermal Cameras: Visualizing Heat for Safety
Thermal cameras capture objects' heat radiation and convert it into thermal images. Widely used in industrial process monitoring, equipment fault detection, and safety inspections, they effectively identify temperature anomalies and potential issues. They are suitable for high-temperature, high-risk environments like building inspections and equipment maintenance.
GigE Vision Cameras: High-Speed, Long-Distance Transmission
GigE Vision cameras utilize Gigabit Ethernet technology for high-speed image data transmission, supporting long-distance transmission up to 100 meters. Suitable for applications requiring real-time data transmission, they are easily integrated into existing Ethernet infrastructure. They are commonly used in industrial automation, quality control, and robotic vision systems.
The Role of Machine Vision Cameras Across Industries: Revolutionizing Retail, Warehousing, and Healthcare
In today's business environment, machine vision cameras play an increasingly important role, offering numerous advantages across various industries. Let's explore some prominent application areas highlighting their versatility and value.
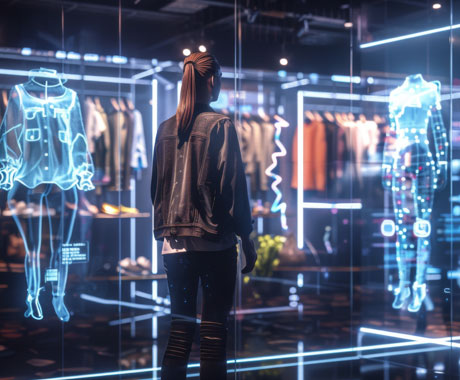
Retail: Enhancing Efficiency and Customer Experience
Machine vision cameras are used in automated checkout systems, quickly scanning and identifying products without manual input, ensuring transaction accuracy and efficiency. They also monitor shelves and product displays, detecting empty spaces, misplaced items, or low inventory, triggering automatic alerts or reordering processes to maintain optimal product availability.
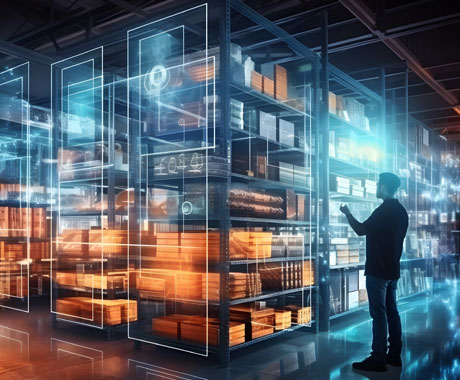
Warehousing and Distribution: Streamlining Operations
In warehouses and distribution centers, machine vision cameras are crucial for automated sorting systems. They capture images or read barcodes to identify and track packages, efficiently sorting and routing items to designated locations. Cameras also inspect incoming and outgoing goods, identifying damaged or defective items to ensure only high-quality products are shipped to customers, reducing returns or rework.
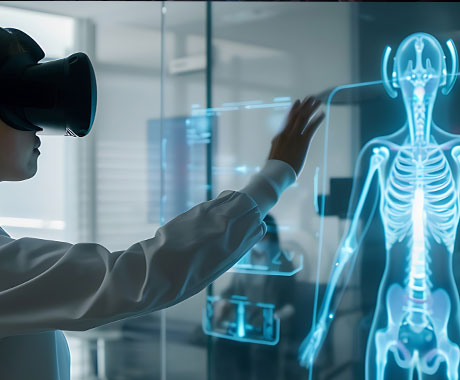
Healthcare: Advancing Diagnostics and Automation
Machine vision cameras are used in medical imaging systems like X-rays, ultrasounds, or endoscopic examinations, capturing detailed images of the human body to aid in diagnosis, surgical procedures, and treatment planning. They also play a vital role in laboratory automation, assisting with sample identification, classification, and analysis, improving the efficiency and accuracy of laboratory processes.
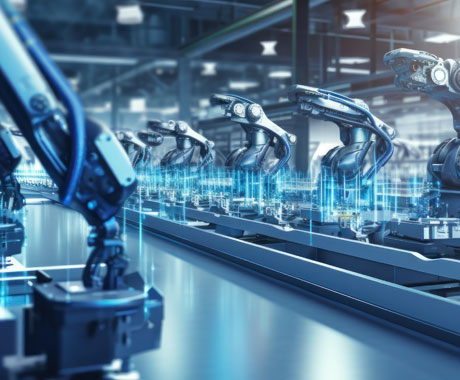
Manufacturing: Ensuring Quality and Precision
Widely used for quality inspection in manufacturing, machine vision cameras detect defects in the production process, measure dimensions, and identify product inconsistencies. This ensures adherence to quality standards, reduces waste or rework, and enhances overall product quality. Cameras also provide visual feedback for vision-guided robotics (VGR), enabling precise positioning, manipulation, or assembly of components, helping robots perform complex tasks accurately and efficiently.
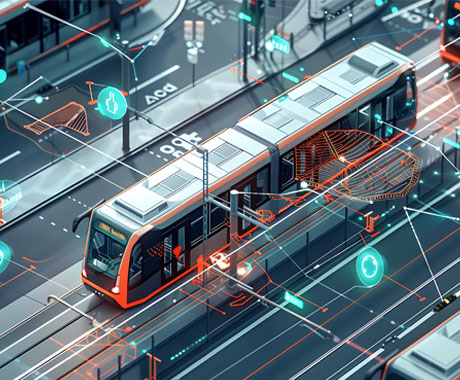
Transportation and Logistics: Optimizing Parcel Handling
Machine vision cameras are applied in automated parcel sorting systems at transportation and logistics facilities. By reading barcodes, capturing images, or extracting information from shipping labels, they accurately sort packages and route them to the correct destinations. Camera technology is also used in vehicle inspection, such as automatic license plate recognition or identifying container numbers on trucks, ensuring fleet safety, compliance, and efficient management.
Latest Trends in Machine Vision Camera Technology: Staying Ahead of the Curve
Machine vision technology continues to evolve. Here are some of the current major technological trends:
- High-Speed Camera Technology
With continually increasing frame rates, some high-speed cameras now achieve tens of thousands of frames per second, suitable for inspections on high-speed production lines like semiconductor chip manufacturing.
- Embedded Vision Systems
Integrating image processing capabilities directly into cameras reduces dependence on external computing resources and improves system response time.
- Multispectral Imaging
This technology goes beyond the traditional RGB range, capturing a wider spectrum of light information. It's widely applied in agriculture, food safety, and material analysis.
- Artificial Intelligence Integration
Cameras with built-in AI processing chips enable edge computing, performing complex tasks like real-time object recognition and defect detection.
- New Sensor Technologies
Event cameras (neuromorphic cameras) only output data when pixel brightness changes, suitable for high dynamic range scenes, significantly reducing data volume.
- Light Field Cameras
These cameras capture information about the direction and intensity of light, allowing post-capture focusing and depth estimation, suitable for 3D reconstruction and virtual reality applications.
Why Connectors and Cables Matter: The Impact of Connectivity on Machine Vision Systems
The choice of connectors and cables is crucial to the performance and stability of machine vision systems. Here are key considerations:
- Signal Integrity: Ensuring Undistorted Data
High-quality connectors and cables are essential for undistorted signals during high-speed image transmission. In applications requiring high data transmission speeds—like 3D cameras, hyperspectral cameras, and smart cameras—using high-performance connectors such as USB 3.0, GigE, or CoaXPress effectively prevents signal loss.
- Interference Resistance: Stability in Harsh Environments
Industrial settings often have significant electromagnetic interference (EMI). Choosing cables and connectors with excellent shielding ensures stable image transmission and prevents data interference during transmission.
- Durability and Flexibility: Extending System Lifespan
Cable cables must withstand repeated bending and stretching in applications like robotic arm-camera systems. Selecting industrial-grade cables with high flexibility and wear resistance extends the system lifespan and ensures long-term stable operation.
Connectivity Standards in Machine Vision: Which is Right for Your Application?
Multiple connector and cable standards are available, each with unique advantages and suitable applications.
- USB3 Vision
- Features: Based on USB 3.0 interface, supports up to 5 Gbps transmission rate.
- Advantages: Wide compatibility, plug-and-play.
- Considerations: Cable length is usually limited to under 5 meters.
- GigE Vision
- Features: Based on Gigabit Ethernet, supports long-distance transmission up to 100 meters.
- Advantages: Cost-effective, easy network integration.
- Considerations: Higher CPU load.
- Camera Link
- Features: Designed specifically for machine vision, supports a high bandwidth of up to 6.8 Gbps.
- Advantages: Low latency, and excellent real-time performance.
- Considerations: Requires dedicated frame grabbers, higher cost.
- CoaXPress (CXP)
- Features: Uses coaxial cables, and supports high-speed transmission (CXP-12 reaches 12.5 Gbps per connection).
- Advantages: Strong long-distance transmission over 100 meters.
- Considerations: Requires specialized hardware, higher initial cost.
- MIPI CSI-2
- Features: Used in embedded systems and mobile devices.
- Advantages: Low power consumption, suitable for battery-powered devices.
- Considerations: Short transmission distances, primarily for board-level connections.
Overcoming Practical Connectivity Challenges: Solutions for Real-World Applications
Machine vision systems face various connectivity challenges. Here's how to address them:
- High-Speed Data Transmission
- Challenge: High-resolution cameras generate large data volumes, increasing the need for high-speed transmission.
- Solution: To ensure rapid image data transfer, opt for connectors supporting high bandwidth, like USB 3.1 Gen 2 or 10G Ethernet.
- Long-Distance Applications
- Challenge: Some industrial environments require long-distance image data transmission.
- Solution: Use fiber optic connectors and cables to prevent signal attenuation over long distances, ensuring data integrity.
- Harsh Environmental Conditions: Industrial settings may involve temperature fluctuations, vibration, and chemical exposure.
- Temperature Fluctuations: Choose industrial-grade connectors and cables with wide temperature ranges.
- Vibration and Shock: Employ connectors with locking mechanisms, like M12 connectors, to prevent loosening or damage.
- Chemical Corrosion: Select materials resistant to corrosion, such as stainless steel or those with protective coatings.
Best Practices for System Integration and Maintenance: Ensuring Long-Term Stability
Implementing best practices ensures the long-term stable operation of machine vision systems.
- Optimize System Integration
- Plan Cable Layouts Carefully: Avoid routing signal cables parallel to power cables to reduce interference.
- Use Cable Management Systems: Keep cables organized for easier maintenance and inspection.
- Ensure Connector Accessibility: Place connectors in accessible locations during the design phase.
- Troubleshoot Common Issues
- Signal Loss or Instability: Check for loose connectors or damaged cables.
- Image Quality Degradation: Verify shielding to address potential EMI interference.
- Performance Decline: Replace aging cables or oxidized connectors as needed.
- Regular Preventive Maintenance
- Scheduled Inspections: Regularly check connector tightness, especially in high-vibration environments.
- Test Cable Integrity: Use professional tools to detect potential problems early.
- Implement Strain Relief: Use strain relief devices in high-stress areas to extend cable life.
Enhance Your Machine Vision System Today
Selecting the right connectors and cables is crucial to unlocking your machine vision system's full potential. As technology advances, staying informed about the latest connectivity solutions positions your operations for greater efficiency, reliability, and success. Don't let subpar connectivity hold back your system's performance—invest in quality components and proactive maintenance to ensure your machine vision applications run smoothly and effectively.
Recommended Connectivity Products for Machine Vision Systems
To support the various connectivity needs in machine vision applications, here are some recommended product lines that cater to different interface standards and environmental requirements:
RJ45 with PoE++ (Power over Ethernet)
PoE++ technology allows for power delivery up to 90W through Ethernet cables, making it ideal for high-power devices in machine vision systems.
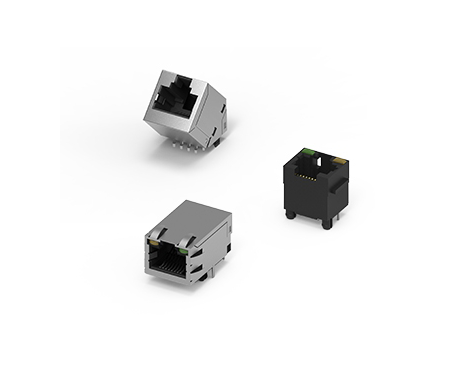
- Features ruggedized designs for industrial environments
- Supports various PoE standards including PoE++
- Available in shielded and unshielded versions for different EMI requirements
USB 3.1 Type-C Connectors
USB 3.1 Type-C connectors offer high-speed data transfer rates up to 10 Gbps, making them suitable for high-resolution camera interfaces.
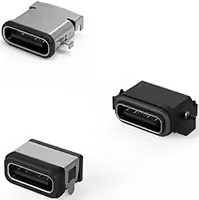
ATTEND USB Type-C Connector Series
- Supports USB 3.1 Gen 2 speeds
- Available in various mounting styles for different PCB designs
- Some models feature waterproof designs for harsh environments
M.2 Connectors for Wi-Fi Modules
M.2 connectors play a crucial role in machine vision systems by enabling the integration of Wi-Fi modules, which are essential for wireless connectivity in modern industrial environments.
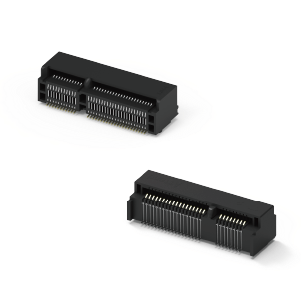
ATTEND M.2 (NGFF) Connector Series
- Supports Key E configuration, specifically designed for Wi-Fi and Bluetooth modules
- Available in different sizes to accommodate various M.2 Wi-Fi module lengths (2230, 2242, 2260, 2280)
- Ensures reliable connections for stable wireless communication in industrial settings
- Enables easy integration and upgradability of wireless capabilities in machine vision systems
FAKRA Connectors
FAKRA connectors are widely used in automotive vision systems for their robust design and color-coding system.
.png)
- Meets USCAR-17 requirements for automotive applications
- Available in various colors for easy identification of different systems
- Provides excellent RF performance up to 6 GHz
M8/M12 Connectors
M8 and M12 connectors are favored in industrial machine vision applications for their rugged design and resistance to environmental factors.
.png)
ATTEND M8/M12 Connector Series
- IP67 rated for protection against dust and water ingress
- Available in various pole configurations to suit different signal requirements
- Supports protocols such as Ethernet and PROFINET for industrial networking
These connector solutions from ATTEND offer high reliability and performance for various machine vision applications, from industrial automation to automotive systems. When selecting connectors for your specific machine vision project, consider factors such as data transmission speed, power requirements, environmental conditions, and system integration needs.