Industrial System Miniaturization and the M8 Connector Revolution
When Equipment Volume Reduces by 40%, Connector Selection Must Also Evolve
Driven by Industry 4.0 initiatives, a wave of equipment miniaturization is transforming global manufacturing. Industry research reports indicate that over the past decade, industrial equipment volumes have commonly reduced by 30-50%. However, as equipment becomes increasingly compact, connector selection has become more critical than ever before.
As factory automation advances toward distributed control architectures and edge detection technologies, small modules and high-density equipment deployments have become the norm. This evolution presents multiple challenges for connector design: extremely limited installation space while requiring highly stable connections; increasingly prevalent high-vibration and high-contamination environments; growing demands for integrated power and data transmission; diverse connector specifications creating integration and maintenance complexities. In this environment, M8 connectors have emerged as an ideal choice for the Industry 4.0 era due to their unique advantages.
M8 Connectors: Industrial-Grade Stability in Compact Design
"The market is no longer satisfied with merely functional capability, but increasingly demands miniaturization, standardization, and industrial durability," states ATTEND's Technical Product Manager. This explains why M8 connectors are gaining increasing recognition in modern industrial applications.
Practical Comparison: Technical Differences Between M5 / M8 / M12
When selecting circular connectors, finding the optimal balance between size, electrical carrying capacity, and vibration resistance stability is essential. Below is a detailed comparison of the three mainstream specifications:Type | Diameter | Current/Voltage Capacity | Common Applications | Technical Advantages | Suitable Scenarios |
---|---|---|---|---|---|
M5 | Ø5 mm | <1 A / 30 V | Ultra-compact sensors, LED indicators | Smallest size, low cost | Low power, extremely space-constrained |
M8 | Ø8 mm | ~3 A / 60 V | Sensors, I/O modules, positioning devices | Compact size, waterproof locking, SPE support | Medium power, balanced applications |
M12 | Ø12 mm | Up to 12 A (coding dependent) | Motors, Ethernet, industrial power | High power, multiple codings, strong EMI protection | High power, standard industrial applications |
In high-vibration environments (such as robotic arms or packaging line equipment), M5 connectors exhibit poor contact stability, while M12 connectors occupy excessive space. M8 connectors provide stable connections with locking mechanisms, balancing size and reliability, making them the ideal choice for medium-load applications.
Application Case: Connector Upgrade in Smart Logistics Sorting Systems
Using smart logistics sorting systems as an example best demonstrates the practical value of M8 connectors. In automated sorting system upgrade projects at large e-commerce logistics centers, such systems typically face the following technical challenges:.png)
Extremely high sensor density, with each conveyor belt requiring configuration of up to 50 detection points (weight, dimensions, barcode scanning); severe space constraints, with multi-level conveyor belt designs limiting connector installation space to less than 15mm; 24/7 high-intensity operation, where poor contact in continuous vibration environments directly affects sorting accuracy; extremely short maintenance windows, with statistics showing that each hour of downtime affects the processing capacity of tens of thousands of packages.
Traditional M12 connectors, while reliable, occupy excessive space during high-density deployment, and wiring complexity increases dramatically with sensor quantity. In such application environments, ATTEND M8 A-code cables and SPE Hybrid solutions can provide the following advantages:
- Enhanced Deployment Density - M8 compact design enables installation of more sensors per unit space, effectively utilizing limited mounting areas
- Simplified Wiring Engineering - SPE Hybrid integrates data and power transmission in a single cable, significantly reducing wiring complexity and installation time
- Improved System Stability - Threaded locking design provides reliable connections in high-vibration environments, reducing system failures caused by poor contact
- Reduced Maintenance Costs - Standardized connector specifications simplify parts management and reduce maintenance hours and associated costs
ATTEND M8 Cable Series: Engineered for Compact Equipment
ATTEND's M8 Connector Cable series is specifically designed for industrial scenarios requiring space-constrained yet high-reliability applications. This series not only inherits the core advantages of M8 connectors but also demonstrates deep understanding of modern industrial requirements through its product design.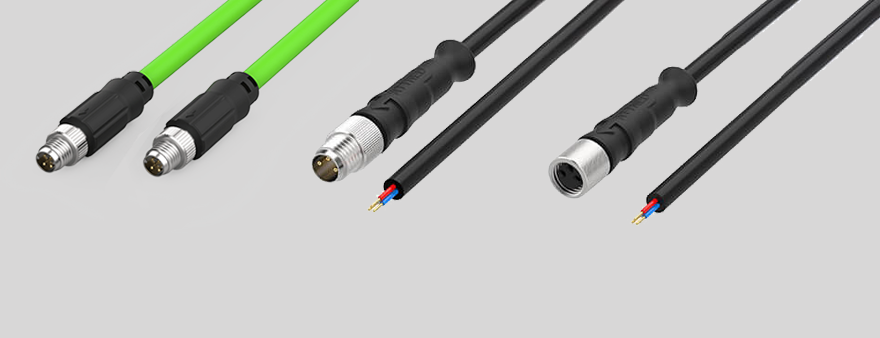
- A-code (3/4-pin) male/female connector pigtail options
- SPE Hybrid variants integrating Single Pair Ethernet and power transmission
- IP67 protection rating + threaded locking design for effective vibration and water resistance
- Compliance with international standards IEC 61076-2-104 (A-code) and IEC 63171-6 (SPE)
Detailed Technical Specifications:
Item | Specification |
---|---|
Compliance Standards | IEC 61076-2 (A-code), IEC 63171-6 (SPE) |
Locking Structure | IP67 + vibration-resistant threaded locking |
Mating Cycles | >100 cycles (SPE: 100 cycles) |
Operating Temperature | –40°C to 85°C (SPE: –40°C to 80°C) |
Conductor Specification | A-code: AWG24 / 0.25 mm²; SPE: AWG26x1P + AWG18x2C |
Cable OD | A-code: 4.2–4.8 mm; SPE: 6.2–6.8 mm |
Termination | Soldering + injection molding |
Vibration Resistance | Complies with IEC 60512-6-4 multi-axis vibration test standards |
Technical Terminology
To help readers better understand product specifications, the following are explanations of key technical terms:- AWG (American Wire Gauge) - American wire gauge standard; smaller numbers indicate thicker wires with higher current-carrying capacity
- OD (Outer Diameter) - Cable outer diameter, affecting space allocation and bend radius design
- SPE (Single Pair Ethernet) - Next-generation industrial communication technology enabling data and power transmission over a single wire pair
- EMC (Electromagnetic Compatibility) - The ability of equipment to function normally in electromagnetic environments without causing electromagnetic interference
Future Outlook: The New Role of Connectors in Industry 4.0
As industrial systems accelerate toward modularization and smart manufacturing, connectors are no longer merely auxiliary components but critical elements of system reliability. M8 connectors are becoming an important choice for modern industrial wiring due to their excellent balance between size and performance.
Under Industry 4.0 development trends, equipment intelligence levels continue to rise, placing increasingly demanding requirements on connectors. From simple electrical connections to integrated data and power transmission, from standardized interface design to reliable performance guarantees in harsh environments, the M8 connector series provides comprehensive and economical solutions.
Whether for sensor integration, I/O module connections, or emerging SPE hybrid transmission applications, the M8 series provides reliable connectivity foundations for modern industrial automation through its compact size, stable performance, and excellent cost-performance ratio. As technology continues to advance and application scenarios expand, M8 connectors will undoubtedly play an increasingly important role in Industry 4.0 development.